Unitized Frame Mechanical Press NS2 Two-Point, From 110 - 300 Tons
Press Information
Press Information & Overview
Two-Point Unitized Frame Stamping Presses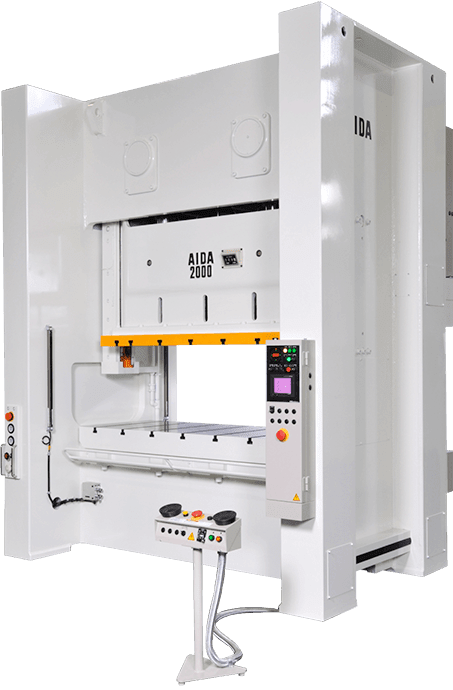
- Highly rigid frame
- Fast acting HOLP system (10 msec)
- AIDA Wet clutch and Brake
- 6-Point full length Bronze Gibs
- Brake stop-time monitoring display
- Automatic lubrication system for Gibs and Crankshaft Bearings
- AIDA MPC safety controller
- Quill mounted flywheel with a flywheel brake
- AC variable frequency drive
AIDA NS2, two-point unitized frame mechanical presses are available from 110 through 300 tons capacity. The six-point slide guide system provides a long useful life. The wet-type clutch and brake provide higher intermittent rates and long life - important factors for hand-fed and top-stop applications.
An AC Variable frequency drive allows for wider speed ranges. The Quill mounted flywheel results in a larger bearing surface. The front to back mounted forged steel crankshaft along with hardened and precision ground gears are well suited for high stress blanking applications. Micro-Inching provides die setting at very low speeds. Additionally, an extensive spare parts inventory in Dayton, OH ensures continuous product support.
With nearly 7,000 AIDA servo and mechanical presses and forming system equipment installations in North America, it is easy to see that AIDA presses are an industry standard.
Press Features
AIDA NS2 Unitized Frame Press Features
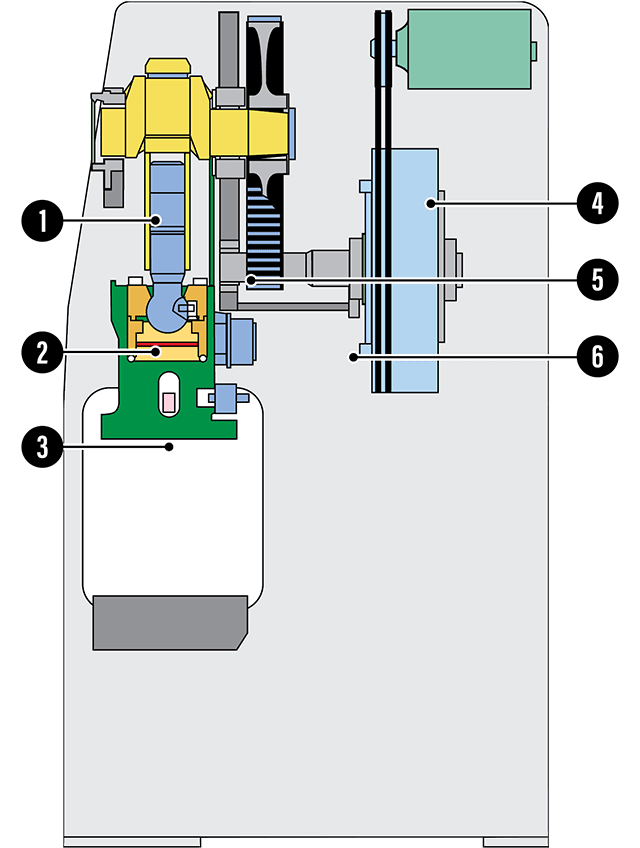
- Ball and Socket Connections
- Hydraulic Overload Protection System (HOLP)
- Recirculating Lubrication System
- AIDA Wet Clutch and Brake
- Hardened & Ground Pinion / Ground Main Gear
- Quill Mounted Flywheel
- Additional Features & Benefits
- Installation and service support by AIDA factory trained technicians
- Highly rigid frame
- Flywheel brake
- Counterbalance lube pump
- Air blow-off with solenoid valve
- ASME certified air tanks
- Full length 6-point slide guides
6-Point Slide Guide System
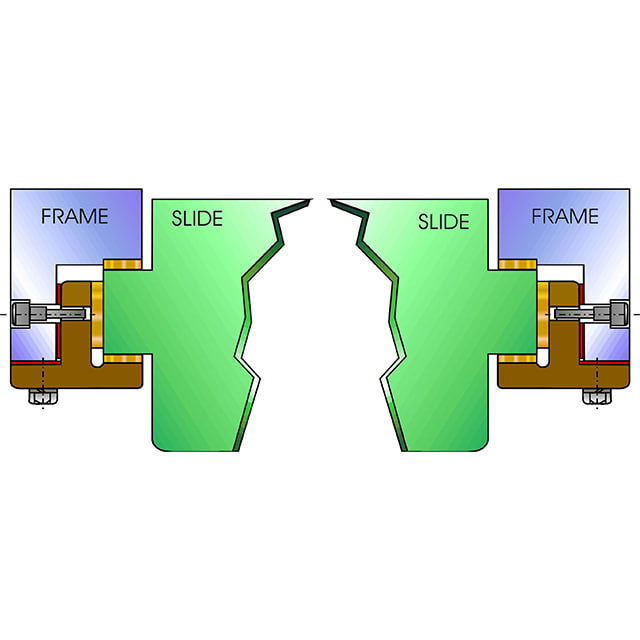
Extra-long gibs with extensions on the slide minimize "tipping" of the slide within the guides and provide superior off-center guiding vs. industry standard
AIDA Wet Clutch and Brake
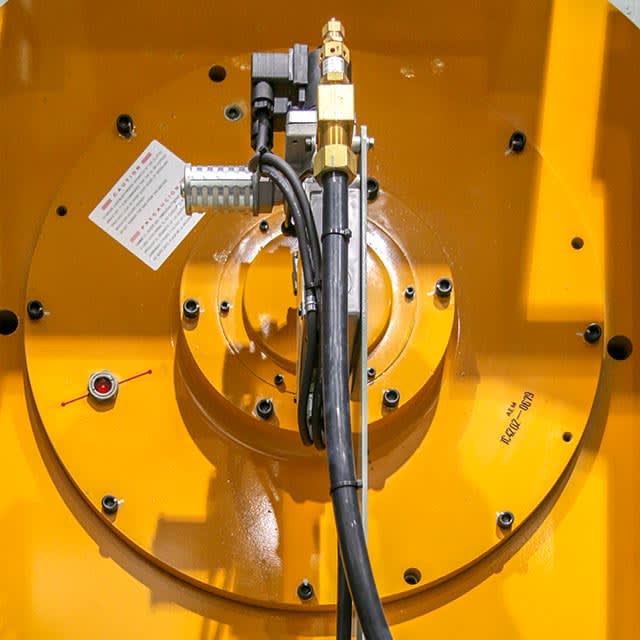
High performance torque transmission system for mechanical press drives. Very little heat generation and component wear so performance does not deteriorate over time.
Ball and Socket Connections
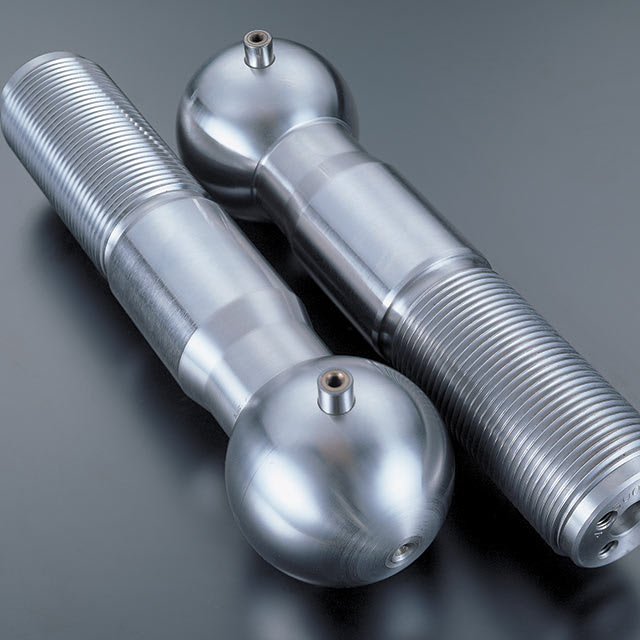
Eliminate one of the largest maintenance costs of a stamping press: the wrist pin slide connections. Designed to withstand the rigors of heavy stamping.
High Precision Drivetrain System
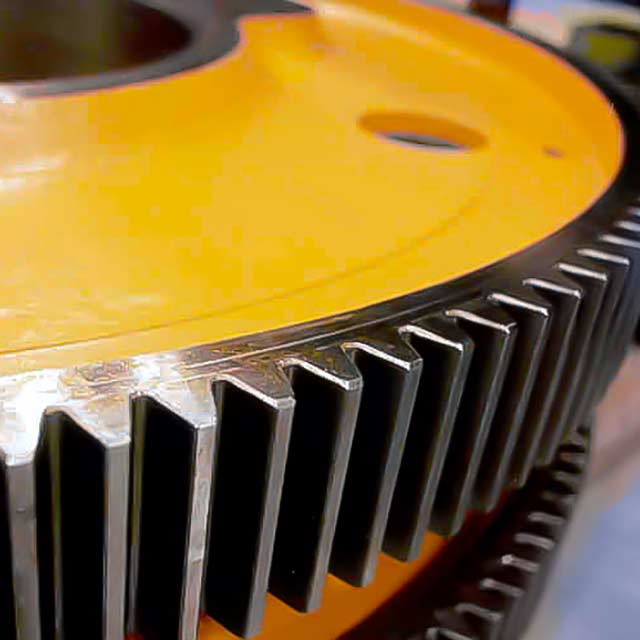
Provides industry minimal backlash resulting in improved press accuracy. Integrated hardened pinion minimizes required gear diameters and related drivetrain inertia.
HOLP
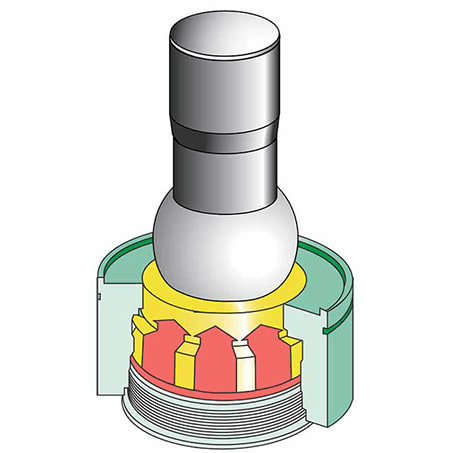
AIDA's press technology - the industry's fastest protection system. When overload occurs, oil evacuates 360 degrees around the ball seat with minimum oil flow resistance as compared to conventional systems
Quill Mounted Flywheel
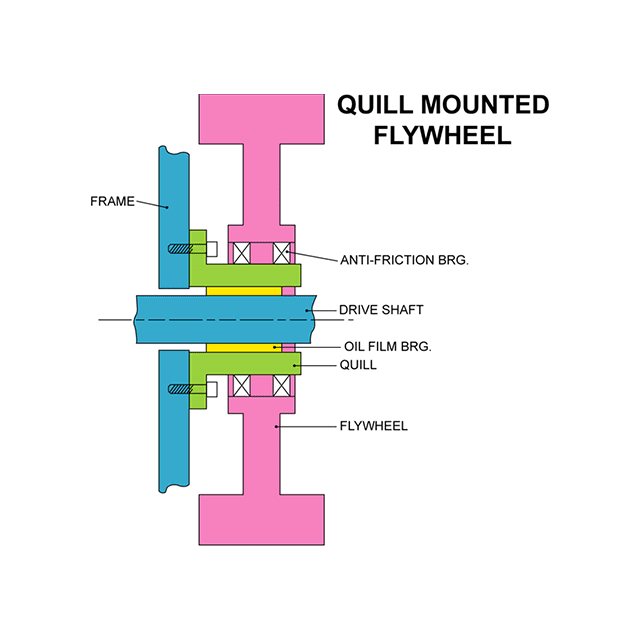
The flywheel is mounted on a quill that is attached to the press frame. The driveshaft passes through the quill and operates in an oil film bearing.
Recirculating Oil Lubrication System
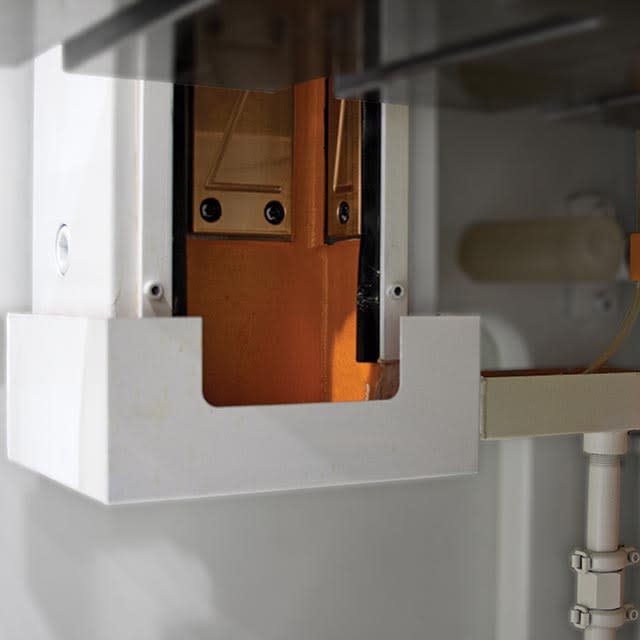
Oil from all lube points is captured, filtered, and recirculated. Bearing points are monitored to ensure that they receive the correct amount of oil.
Press Specifications
NS2 Mechanical Unitized Frame Press Specifications
110 Ton | 160 Ton |
200 Ton | 250 Ton |
300 Ton | Specifications PDF |
110 - 300 Ton | Specifications PDF |
NS2-1100, 110 Ton Mechanical Unitized Frame Press Specifications
NS2 MODELS | |||
Press Technical Data | Unit | NS2-1100 | |
Tonnage Capacity | kN | 1100 | |
U.S. ton | 121 | ||
Rating Point | mm | 5.0 | |
in. | 0.19 | ||
Stroke Length | mm | 110 | |
in. | 4.33 | ||
Strokes per Minute (No Load) | spm | 50~110 | |
Die Height, slide to bolster | mm | 350 | |
in. | 13.78 | ||
Slide Adjustment | mm | 90 | |
in. | 3.54 | ||
Slide Area (LR x FB) | mm | 1360 x 520 | |
in. | 53.54 x 20.50 | ||
Bolster Area (LR x FB) | mm | 1660 x 680 | |
in. | 65.40 x 26.80 | ||
Side Opening (W x H) | mm | 700 x 285 | |
in. | 27.6 x 11.2 | ||
Bolster Thickness | mm | 155 | |
in. | 6.10 | ||
Maximum Upper Die Weight | kg | 550 | |
lbs. | 1213 | ||
Main Motor | kW | 11 | |
HP | 15 | ||
Required Air Pressure | Mpa | 0.5 | |
psi | 73 |
NS2-1600, 160 Ton Mechanical Unitized Frame Press Specifications
NS2 MODELS | |||
Press Technical Data | Unit | NS2-1600 | |
(1) | (2) | ||
Tonnage Capacity | kN | 1600 | |
U.S. ton | 176 | ||
Rating Point | mm | 6.0 | |
in. | 0.23 | ||
Stroke Length | mm | 130 | 200 |
in. | 5.12 | 7.87 | |
Strokes per Minute (No Load) | spm | 40~90 | 30~60 |
Die Height, slide to bolster | mm | 400 | 450 |
in. | 15.76 | 17.72 | |
Slide Adjustment | mm | 100 | |
in. | 3.94 | ||
Slide Area (LR x FB) | mm | 1500 x 580 | |
in. | 59.10 x 22.83 | ||
Bolster Area (LR x FB) | mm | 1800 x 760 | |
in. | 70.90 x 29.92 | ||
Side Opening (W x H) | mm | 780 x 325 | 780 x 375 |
in. | 30.7 x 12.8 | 30.7 x 14.8 | |
Bolster Thickness | mm | 165 | |
in. | 6.50 | ||
Maximum Upper Die Weight | kg | 800 | |
lbs. | 1760 | ||
Main Motor | kW | 15 | |
HP | 20 | ||
Required Air Pressure | Mpa | 0.5 | |
psi | 73 |
NS2-2000, 200 Ton Mechanical Unitized Frame Press Specifications
NS2 MODELS | |||
Press Technical Data | Unit | NS2-2000 | |
(1) | (2) | ||
Tonnage Capacity | kN | 2000 | |
U.S. ton | 220 | ||
Rating Point | mm | 7.0 | |
in. | 0.27 | ||
Stroke Length | mm | 150 | 250 |
in. | 5.91 | 9.84 | |
Strokes per Minute (No Load) | spm | 35~75 | 25~50 |
Die Height, slide to bolster | mm | 450 | 500 |
in. | 17.72 | 19.69 | |
Slide Adjustment | mm | 110 | |
in. | 4.33 | ||
Slide Area (LR x FB) | mm | 1850 x 650 | |
in. | 72.83 x 25.60 | ||
Bolster Area (LR x FB) | mm | 2150 x 840 | |
in. | 84.65 x 33.10 | ||
Side Opening (W x H) | mm | 860 x 365 | 860 x 415 |
in. | 33.9 x 14.8 | 33.9 x 16.3 | |
Bolster Thickness | mm | 170 | |
in. | 6.70 | ||
Maximum Upper Die Weight | kg | 1200 | |
lbs. | 2646 | ||
Main Motor | kW | 22 | |
HP | 30 | ||
Required Air Pressure | Mpa | 0.5 | |
psi | 73 |
NS2-2500, 250 Ton Mechanical Unitized Frame Press Specifications
NS2 MODELS | |||
Press Technical Data | Unit | NS2-2500 | |
(1) | (2) | ||
Tonnage Capacity | kN | 2500 | |
U.S. ton | 275 | ||
Rating Point | mm | 7.0 | |
in. | 0.27 | ||
Stroke Length | mm | 170 | 280 |
in. | 6.70 | 11.0 | |
Strokes per Minute (No Load) | spm | 25~60 | 20~40 |
Die Height, slide to bolster | mm | 450 | 550 |
in. | 17.72 | 21.65 | |
Slide Adjustment | mm | 120 | |
in. | 4.72 | ||
Slide Area (LR x FB) | mm | 2100 x 700 | |
in. | 82.70 x 27.60 | ||
Bolster Area (LR x FB) | mm | 2400 x 920 | |
in. | 94.50 x 36.20 | ||
Side Opening (W x H) | mm | 940 x 355 | 940 x 455 |
in. | 37.0 x 14.0 | 37.0 x 17.9 | |
Bolster Thickness | mm | 180 | |
in. | 7.10 | ||
Maximum Upper Die Weight | kg | 1650 | |
lbs. | 3640 | ||
Main Motor | kW | 30 | |
HP | 40 | ||
Required Air Pressure | Mpa | 0.5 | |
psi | 73 |
NS2-3000, 300 Ton Mechanical Unitized Frame Press Specifications
NS2 MODELS | |||
Press Technical Data | Unit | NS2-3000 | |
(1) | (2) | ||
Tonnage Capacity | kN | 3000 | |
U.S. ton | 330 | ||
Rating Point | mm | 6.0 | |
in. | 0.23 | ||
Stroke Length | mm | 200 | 300 |
in. | 7.87 | 11.81 | |
Strokes per Minute (No Load) | spm | 20~50 | 15~35 |
Die Height, slide to bolster | mm | 600 | 650 |
in. | 23.62 | 25.59 | |
Slide Adjustment | mm | 130 | |
in. | 5.12 | ||
Slide Area (LR x FB) | mm | 2400 x 900 | |
in. | 94.50 x 35.40 | ||
Bolster Area (LR x FB) | mm | 2600 x 1200 | |
in. | 102.40 x 47.20 | ||
Side Opening (W x H) | mm | 1220 x 530 | 1220 x 580 |
in. | 48.0 x 20.9 | 48.0 x 22.8 | |
Bolster Thickness | mm | 200 | |
in. | 7.90 | ||
Maximum Upper Die Weight | kg | 2300 | |
lbs. | 5071 | ||
Main Motor | kW | 37 | |
HP | 50 | ||
Required Air Pressure | Mpa | 0.5 | |
psi | 73 |
NS2, 110 - 300 Ton Mechanical Unitized Frame Press Specifications
NS2 MODELS | ||||||||||
Press Technical Data | Unit | NS2-1100 | NS2-1600 | NS2-2000 | NS2-2500 | NS2-3000 | ||||
(1) | (1) | (2) | (1) | (2) | (1) | (2) | (1) | (2) | ||
Tonnage Capacity | kN | 1100 | 1600 | 2000 | 2500 | 3000 | ||||
U.S. ton | 121 | 176 | 220 | 275 | 330 | |||||
Rating Point | mm | 5.0 | 6.0 | 7.0 | 7.0 | 6.0 | ||||
in. | 0.19 | 0.23 | 0.27 | 0.27 | 0.23 | |||||
Stroke Length | mm | 110 | 130 | 200 | 150 | 250 | 170 | 280 | 200 | 300 |
in. | 4.33 | 5.12 | 7.87 | 5.91 | 9.84 | 6.70 | 11.0 | 7.87 | 11.81 | |
Strokes per Minute (No Load) | spm | 50~110 | 40~90 | 30~60 | 35~75 | 25~50 | 25~60 | 20~40 | 20~50 | 15~35 |
Die Height, slide to bolster | mm | 350 | 400 | 450 | 450 | 500 | 450 | 550 | 600 | 650 |
in. | 13.78 | 15.76 | 17.72 | 17.72 | 19.69 | 17.72 | 21.65 | 23.62 | 25.59 | |
Slide Adjustment | mm | 90 | 100 | 110 | 120 | 130 | ||||
in. | 3.54 | 3.94 | 4.33 | 4.72 | 5.12 | |||||
Slide Area (LR x FB) | mm | 1360 x 520 | 1500 x 580 | 1850 x 650 | 2100 x 700 | 2400 x 900 | ||||
in. | 53.54 x 20.50 | 59.10 x 22.83 | 72.83 x 25.60 | 82.70 x 27.60 | 94.50 x 35.40 | |||||
Bolster Area (LR x FB) | mm | 1660 x 680 | 1800 x 760 | 2150 x 840 | 2400 x 920 | 2600 x 1200 | ||||
in. | 65.40 x 26.80 | 70.90 x 29.92 | 84.65 x 33.10 | 94.50 x 36.20 | 102.40 x 47.20 | |||||
Side Opening (W x H) | mm | 700 x 285 | 780 x 325 | 780 x 375 | 860 x 365 | 860 x 415 | 940 x 355 | 940 x 455 | 1220 x 530 | 1220 x 580 |
in. | 27.6 x 11.2 | 30.7 x 12.8 | 30.7 x 14.8 | 33.9 x 14.8 | 33.9 x 16.3 | 37.0 x 14.0 | 37.0 x 17.9 | 48.0 x 20.9 | 48.0 x 22.8 | |
Bolster Thickness | mm | 155 | 165 | 170 | 180 | 200 | ||||
in. | 6.10 | 6.50 | 6.70 | 7.10 | 7.90 | |||||
Maximum Upper Die Weight | kg | 550 | 800 | 1200 | 1650 | 2300 | ||||
lbs. | 1213 | 1760 | 2646 | 3640 | 5071 | |||||
Main Motor | kW | 11 | 15 | 22 | 30 | 37 | ||||
HP | 15 | 20 | 30 | 40 | 50 | |||||
Required Air Pressure | Mpa | 0.5 | 0.5 | 0.5 | 0.5 | 0.5 | ||||
psi | 73 | 73 | 73 | 73 | 73 |
Technical Resources
Frequently Asked Questions
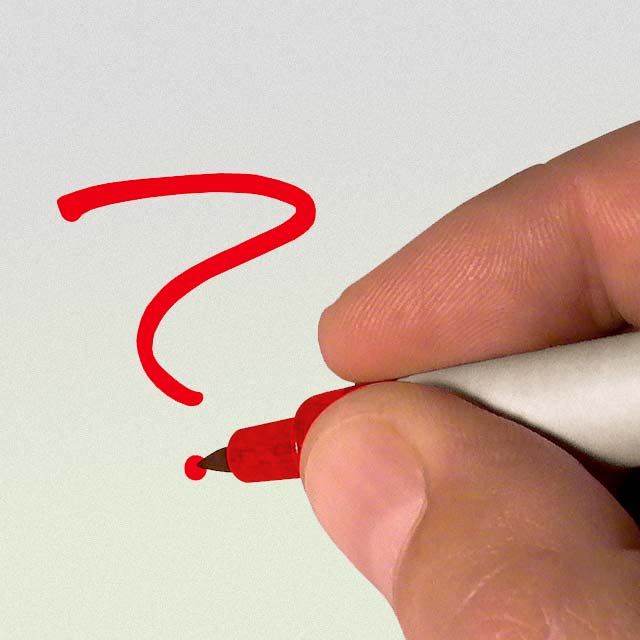
We offer answers for all types of common questions - whether technical in nature or as simple as where to look for career opportunities. Examples of some questions are: What is HOLP? Where is the closest AIDA facility located? How can we get a copy of the manual for our AIDA press? What is reverse tonnage? Visit our frequently answered questions section to find answers to your questions.
View Frequently Asked QuestionsAIDA-Tech White Papers
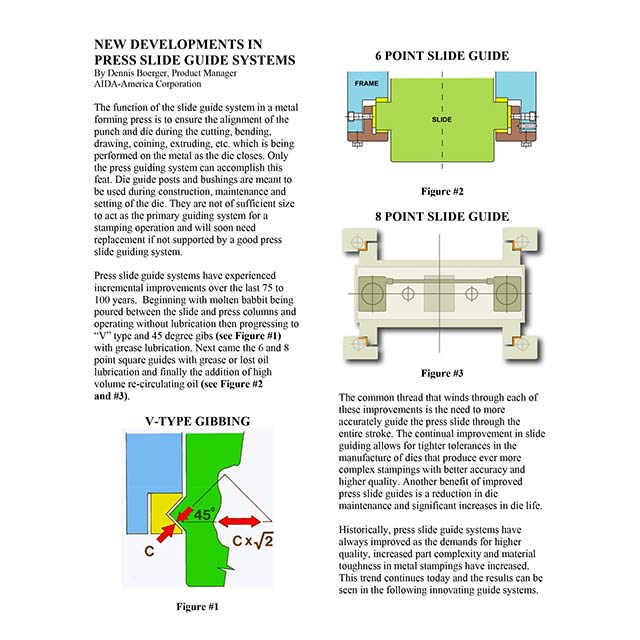
Topics such as connections spacing, slide guiding systems, reverse tonnage and more, AIDA-Tech White papers offer information for a variety of technical subjects related to stamping presses and press operations.
View AIDA-Tech White PapersMetalforming Articles
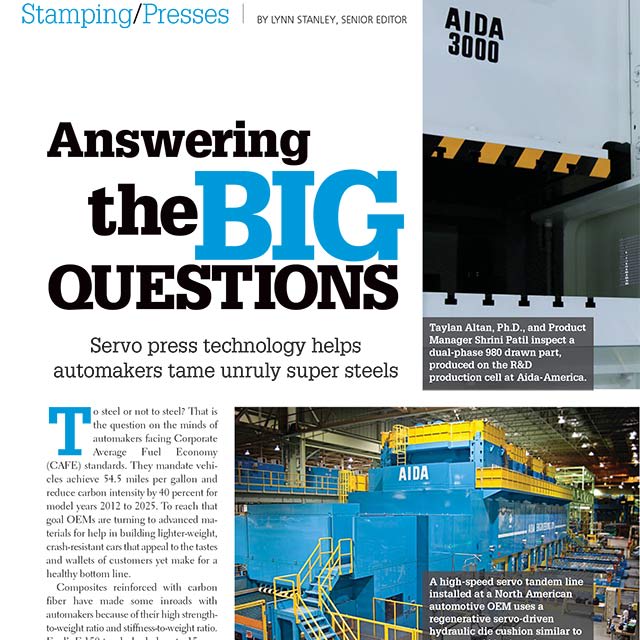
We maintain a library of metalforming articles from a variety of industry publications covering a wide range of topics centered on stamping and press operations. Topics include press technology, market trends, and press applications. Many of the articles collected here have been authored by or contributed to by AIDA associates.
View Metalforming ArticlesAIDA Press User Testimonials
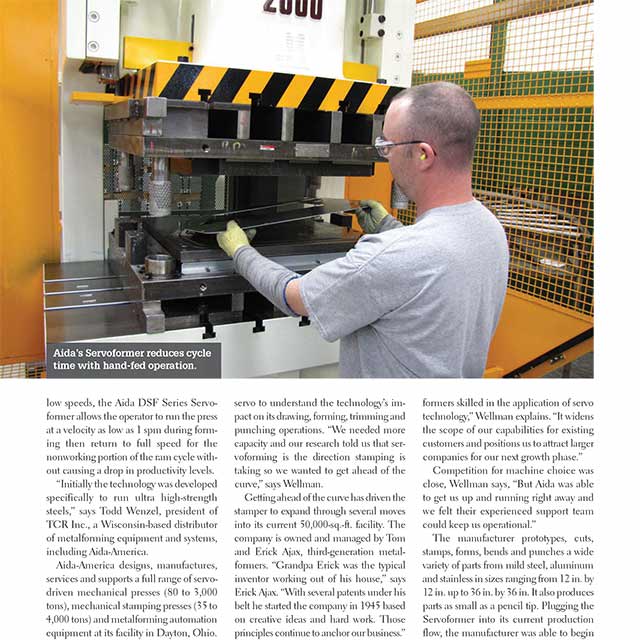
AIDA press users describe their companies and business operations, as well as, how they have used AIDA technology to achieve their production goals and expand their capacity and capabilities. Examples are provided from many different types of companies from job shops, to tier suppliers, to OEMs. Read on to see how leaders in many industries have successfully partnered with AIDA.
View User TestimonialsApplications Studies & Die Trials
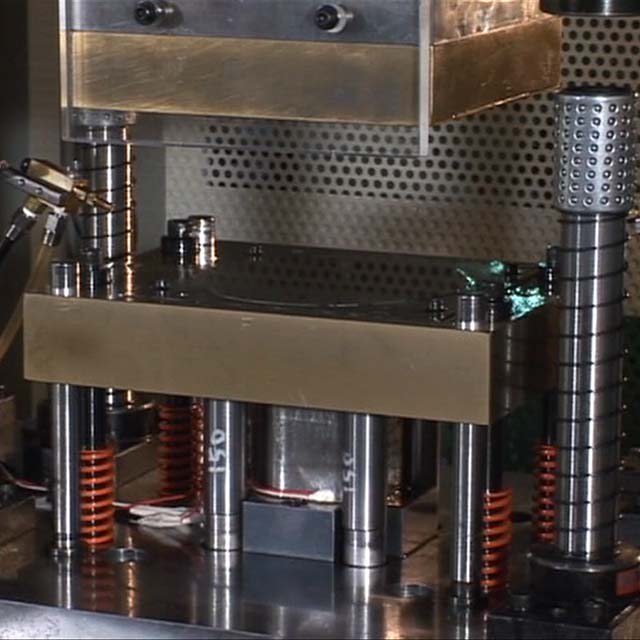
Application studies and die trials provided by AIDA prove, with your own dies and part drawings, how AIDA stamping press technology can have multiple benefits to your manufacturing operations, including increased production rates, higher quality parts, reduced scrap, and reduced maintenance.
Applications Studies & Die TrialsStamping Press Technology
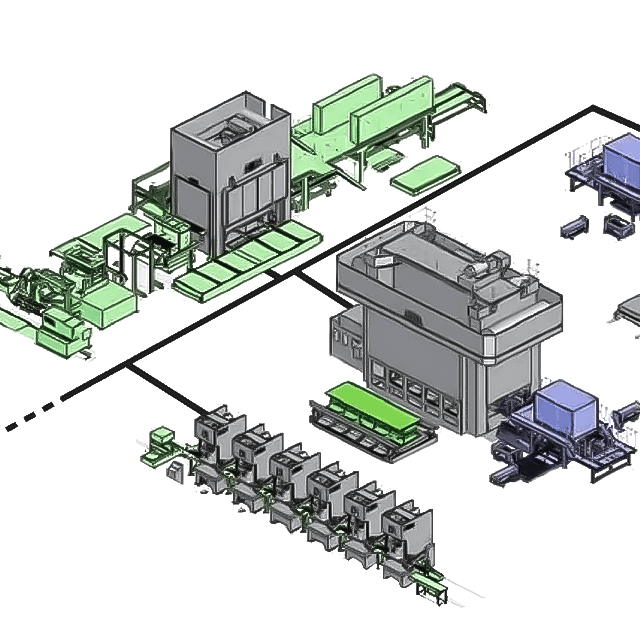
For over 100 years AIDA has been developing and manufacturing specialized metalforming products like metal stamping presses and related automation equipment, such as transfers, robots, and feeders. AIDA's exclusive stamping press technology is used throughout our wide range of presses, from 30 through 4,000 tons capacity.
Stamping Press TechnologyEducational Partners & Resources
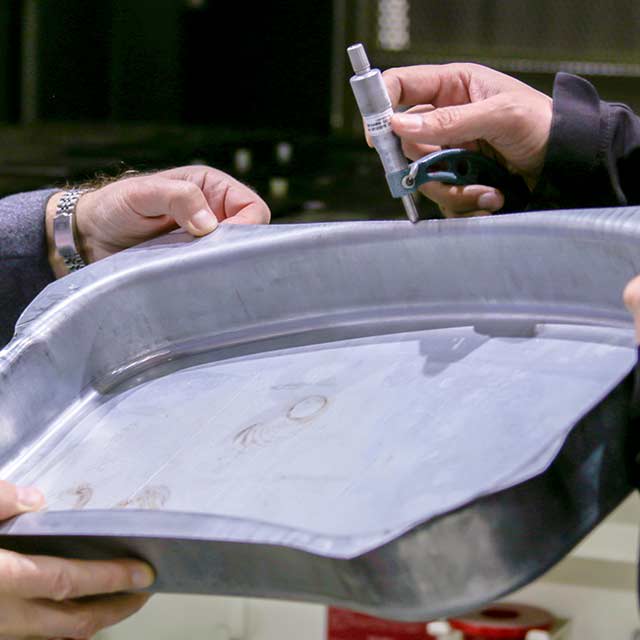
Not only does AIDA invest 5% of annual revenue towards internal research and development, but AIDA also actively seeks and participates in research with educational institutions such as the Center for Precision Forming (OSU), Institut für Umformtechnik, Edison Welding and others.
More About Educational PartnersTerms & Glossary
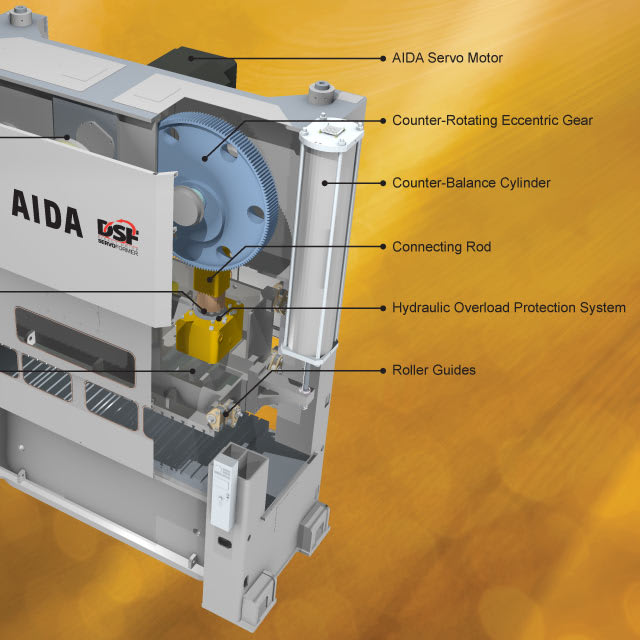
A variety of functions may be performed by many different types of presses, depending upon the tooling. Typical press operations and other terms referring to press features and functions, as well as basic press characteristics and designs are explained in this section of our website.
View Terms & Glossary